Primary sorting screen and optical sorters produce high-quality recyclables to a newly upgraded 30TPH Cal-Waste facility in Galt, CA
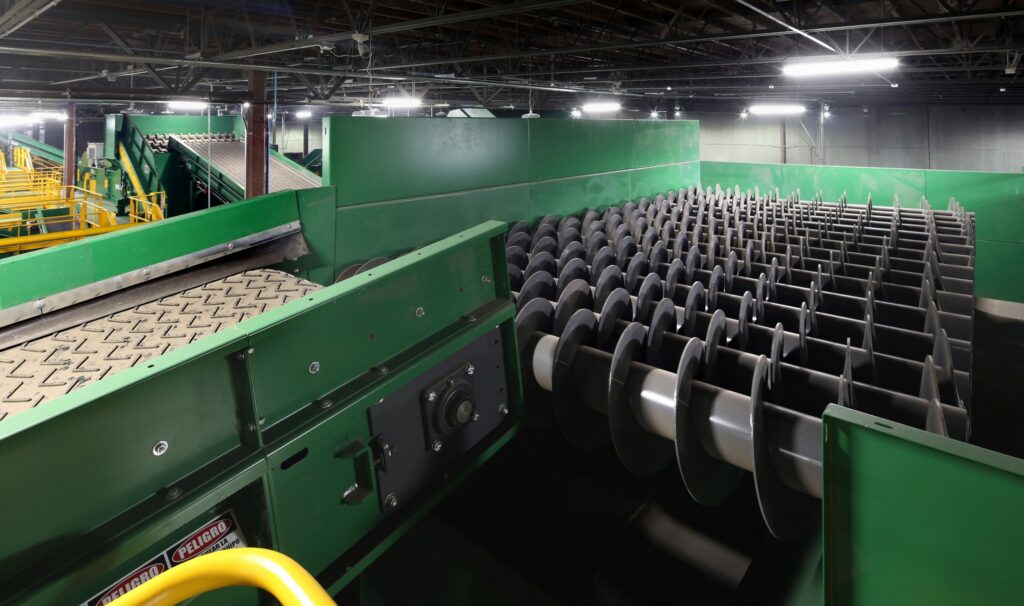
BACKGROUND
Cal-Waste is a California based solid waste collection and processing company that operates several MRF’s in the Central Valley of California. In 2012, Cal-Waste enlisted CP Group to design and install an 11 tons per hour (TPH) facility in Galt, CA. Then in 2019, to meet updated quality standards and throughput demand, Cal-Waste partnered again with their longtime supplier to design and install a new 30 TPH system upgrade.
The new system includes CP Group’s cantilevered auger technology as well as five optical sorters. Because of new technology, automation, and innovative design the facility is now producing high-quality recyclables that are exceeding the market requirements.
Upgrading their state-of-the-art MRF was an investment to better serve their communities and municipalities, provide material buyers higher grade commodities, create a more robust material outlet for haulers, process more material, and provide workers a safer environment.
THE SITUATION
Cal-Waste’s aging system, their need to increase end market purity and decrease manual labor load called for a whole system upgrade to be housed in the same 100,000 SF MRF. They decided to work with their long-time partners at CP Group to develop a new system design that would address all their needs.
CHALLENGE | OBJECTIVE |
System not meeting fiber requirements | Increase purity |
High labor rates and excessive amount of labor | Go from two shifts to one |
Dated system with old technology | System automation |
Small tonnage capacity | Serving a wider area would require taking on more material |
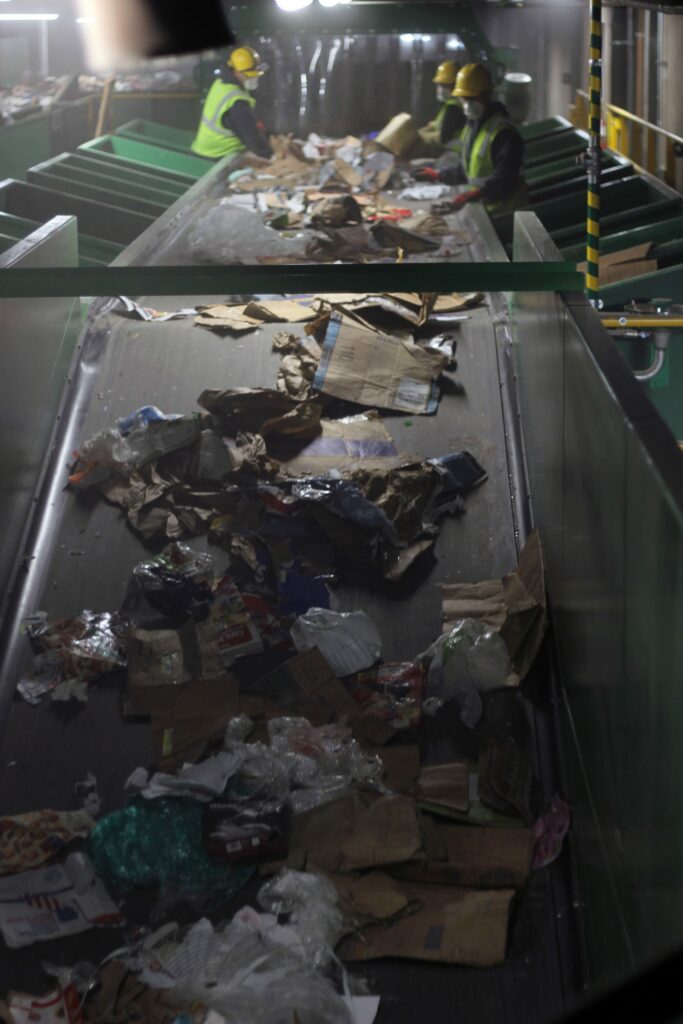
THE SOLUTION
Higher purity was achieved with innovative design, new technology and automation. The new MRF increased processing capacity by 173% (30 tons per hour) but only increased manual sorting headcount by 29%.
Primary Sorter
At the front end of the system directly after the infeed conveyor and prior to the presort is a Primary Auger Screen, a new concept to single stream processing. This primary sorting screen removes the smaller fraction (screen unders) which comprises of approximately 60-65% of the inbound material. Since more than half of the material is diverted, it greatly decreases the burden depth on the presort line and enables manual sorters to be more productive and safer. Additionally, because much of the materials bypasses the manual sorters, fewer people are needed and they can more easily see and pick out the large trash, rigids, and metals. Worker safety is so important. Sorters are much safer because they are not exposed to the smaller fraction which can contain smaller sharps and biohazardous material. Cal-Waste’s progressive transformation is the first in the nation to include this machine at the presort and it has proven successful.
Screens
- A second Auger Screen is used in place of a traditional scalping screen; however, it is extremely low maintenance with no wrapping or jamming and provides a consistent split of material to feed downstream.
- CP OCCScreen utilizes steel discs for low maintenance and efficient removal of OCC.
- CP GlassBreaker Screen which also uses cast-chromium alloys discs for minimal wear and tear while providing high removal of glass and fines.
- For paper screening, the CP AWScreen (anti-wrap screen) has the latest large paper screening technology, and the CPScreen (polishing screen) is the final screening on the small paper. The paper screens use rubber discs to provide the most efficient 2D/3D separation. These discs last 2,000 (CPScreen) and 3,000 (AWScreen) hours. The Cal-Waste facility was designed to operate with minimal maintenance and high automation.
“The Primary Auger Screen takes the burden depth down to a much more manageable level and does a great job of spreading everything out so there are no big lumps and clumps.”
Dave Vaccarezza
Owner, Cal-Waste
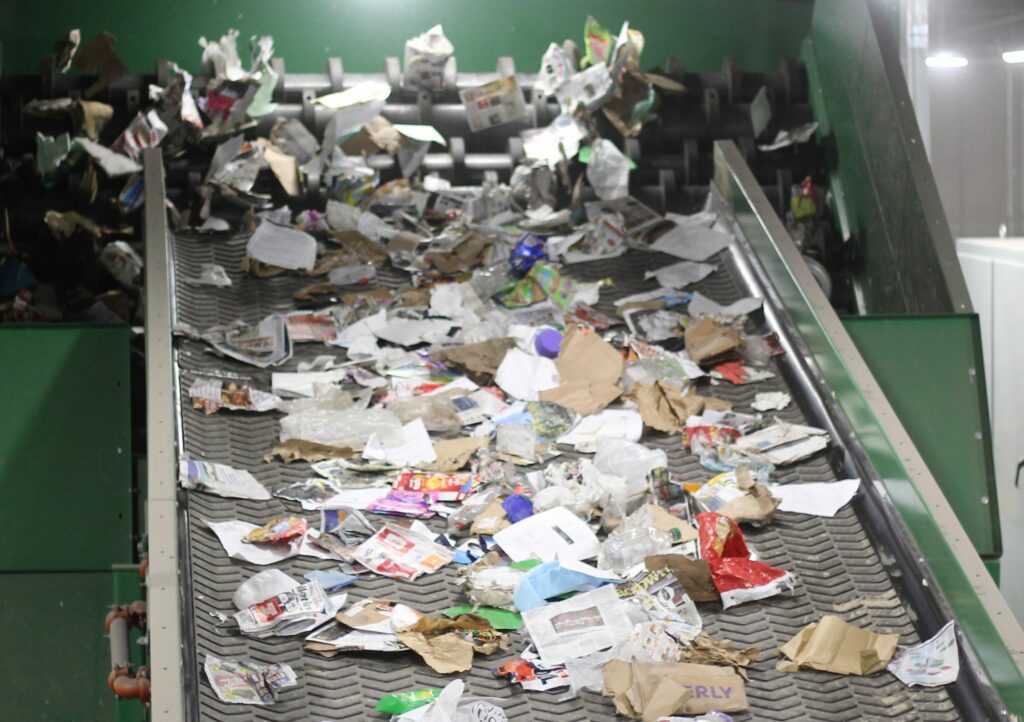
Optical Sorters
The MRF features five MSS optical sorters. Historically the recovery and QC of fiber and container lines were a very manual process. Now they are both automated. The facility features three MSS CIRRUS FiberMax™ optical sorters – one on the overs of the large cut from the AWScreen, one taking the unders of the AWScreen, and one on the overs of the CPScreen. These three FiberMax™ optical sorters perform at 1,000 feet per minute and on average 1,000 picks per minute (the fastest in the industry which equates to higher volume processing).
A typical manual sorter picks 35 picks per minute. The FiberMax™ sorters make it possible for Cal-Waste to achieve their fiber purity goals while keeping a high throughput and without adding manual sorters.
Additionally, there are two PlasticMax™ optical sorters that recover PET, HDPE, and mixed plastics with minimal human intervention.
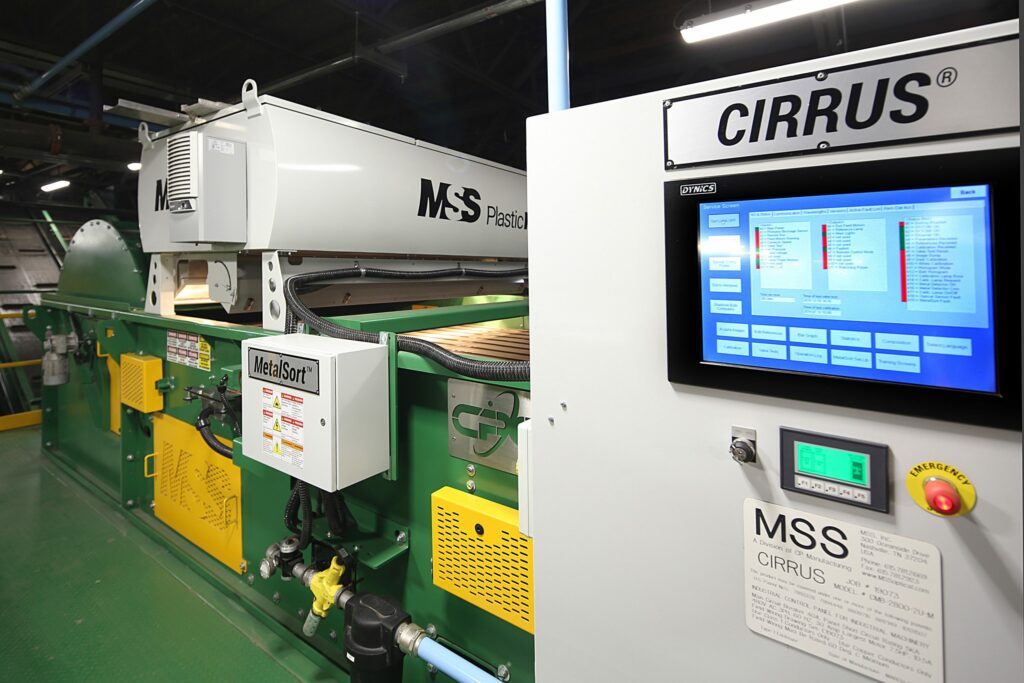
Glass Processing
CP Group installed a Lights Out ADS (air drum separator) for glass processing. This unit carries clean material to an automated glass load out system that self-loads into end dump trailers and residual material self-loads via conveyors.
THE RESULT
With the investment Cal-Waste made into upgrading their MRF, they are better able to serve their communities and municipalities with a state-of-the-art facility, provide their material buyers with higher grade commodities, create a more robust material outlet for haulers, and provide workers with a safer working environment.
Cal-Waste and CP Group completed a performance test to retrieve data and analyze key performance indicators: throughput, system availability, mechanical performance, capture rate efficiencies, and optical performance efficiencies. The performance test was passed with a system availability of 95% and capture rates all above mechanical and optical requirements.
Mechanical Capture Rate
MATERIAL | TEST RATE | OVER REQ. |
Mixed Glass | 99.2% | 4.2% |
Aluminum | 94.4% | 0.4% |
Ferrous Metals | 96.4% | 0.4% |
OCC | 96.2% | 6.2% |
Fiber | 96.4% | 6.4% |
Plastics | 95.5% | 5.9% |
Optical Removal Efficiencies
MATERIAL | TEST RATE | OVER REQ. |
Prohibs, Chip and Browns | 95.7% | 5.7% |
OCC | 94.3% | 4.3% |
Fiber | 98% | 8% |
Plastic | 95.6% | 1.6% |
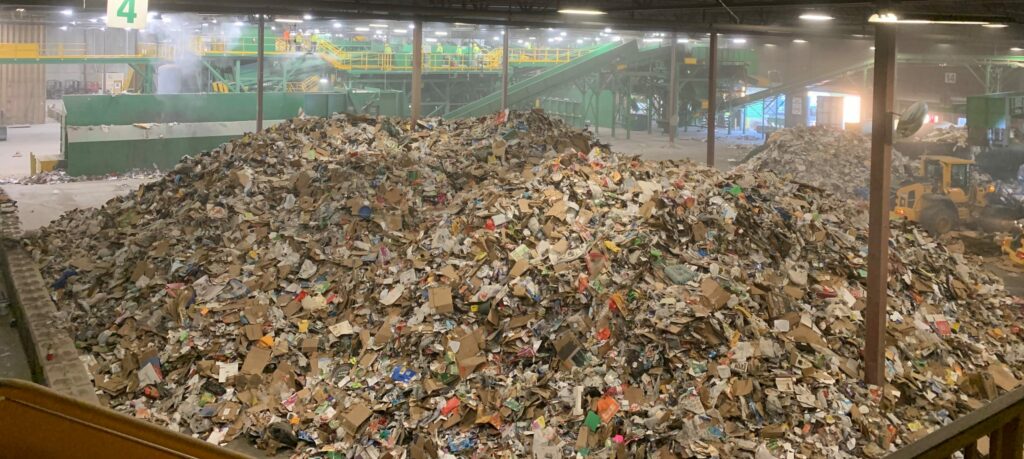
About the Equipment
The CP Auger Srcreen™ sizes material by using a series of cantilevered augers that mitigate wrapping and jamming and require very low-maintenance. As a primary separator, the CP Auger Srcreen™ reduces presort headcount and increases worker safety by bypassing 65%+ of material that manual sorters would typically see, including hazards and sharps.
When used as a scalping or fines screen, similar sized material streams are created to properly feed downstream sorting machines. It captures small OCC (old corrugated containers) in one place for improved recovery and has a tight pattern to remove fines into a separate stream. Built with low-wear technology, it maintains reliable sizing at high volumes for Single Stream, MSW, C&D, C&I, and Green Waste applications.
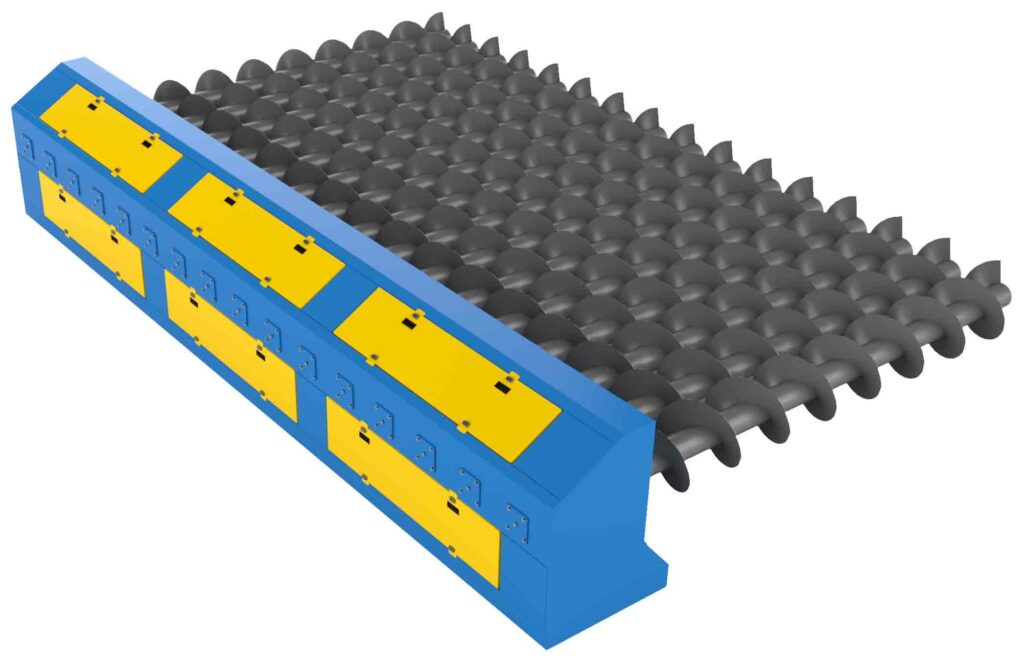
MSS CIRRUS® FiberMax™ optical sorters run at 1,000 feet per minute which is higher than the industry standard for belt speed. This lightens material on the belt and increases accuracy of the by decreasing collateral damage. The higher belt speeds also increase picks per minute. MSS uses their patented PrecisionFlow™ eject hood in combination with air-assist systems for precise material handling of flexible material.
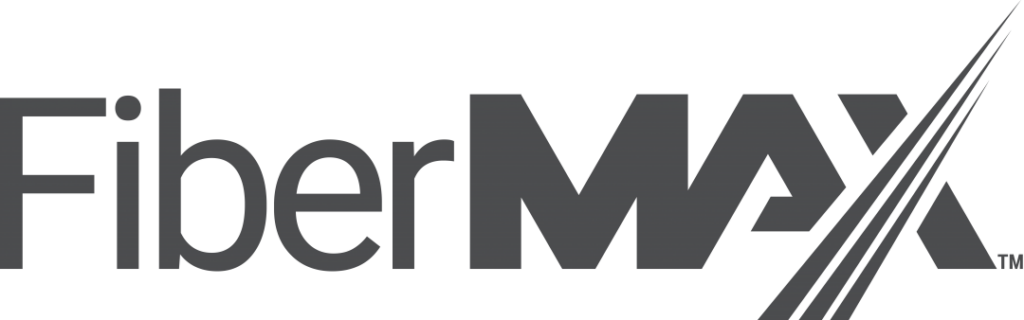
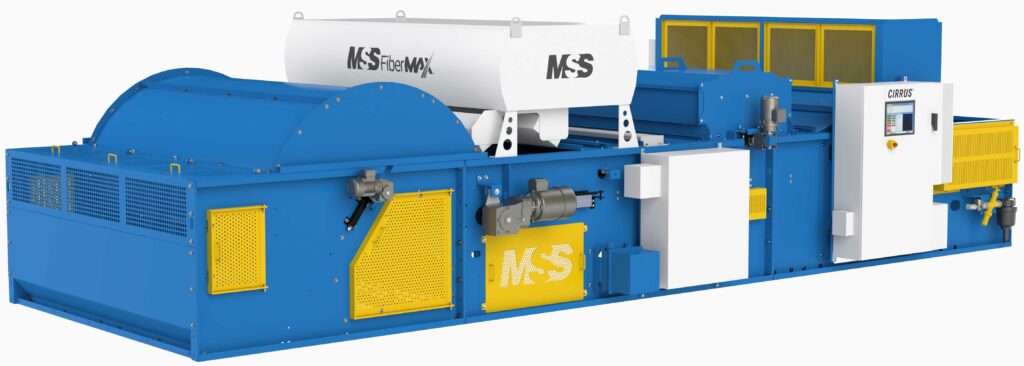
About Cal-Waste
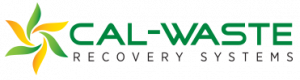
Cal-Waste is a family owned solid waste collection and processing company that has operated in the Central Valley of California since 1927. The company continues to be on the leading edge of innovations in technology and recycling efforts at several MRFs. Cal-Waste has a commitment to the environment and the communities they serve. They successfully permitted one of the first solid-waste facilities in the California that combined the operations of a transfer station, materials-recovery facility, and green waste composting. Cal-Waste has since built three additional recycling facilities. Cal-Waste pioneered one of the very first residential automated three-cart (i.e. trash, yard waste and recycling) programs in the country–resulting in 60 percent less waste going into local landfills each year.