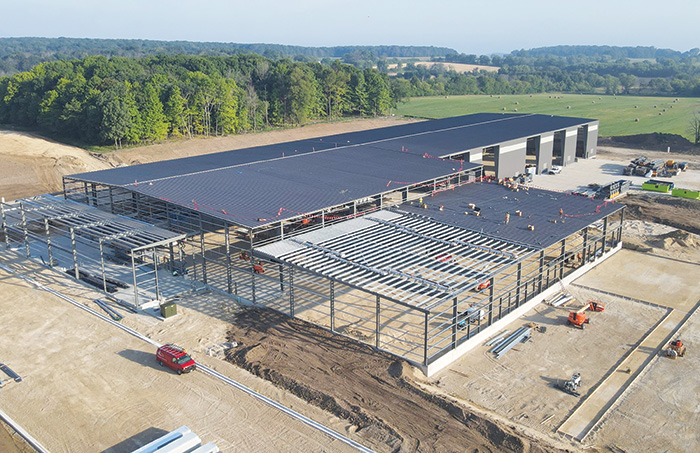
Part 1: Planning, Designing and Constructing Your New Facility Team Selection and Engagement Early in the Process
By: Jeff Eriks, Evan Williams, Ashley Davis and Ryan Fogelman
It is important that you build the right team upfront. This includes internal and external stakeholders, equipment suppliers, additional vendors, the design team, the construction team, and any public entities that may be involved. It is critical that you identify who these team members are and engage them early. This effort on the front end will lead to strong communication for the duration of the project, creating alignment amongst all parties to ensure that the building and equipment are designed to function synonymously. Additionally, the operations team will be able to step in and function in a way that makes the facility cost-effective to operate both in the near term and long term. Soliciting input and feedback later in the process can lead to design changes, budget and schedule impacts, and other ripple effects that can impact project delivery. By working hard to lock in a well-defined scope early in the process, you can minimize surprises and late-stage changes that can impact the success of the project.
Site Selection
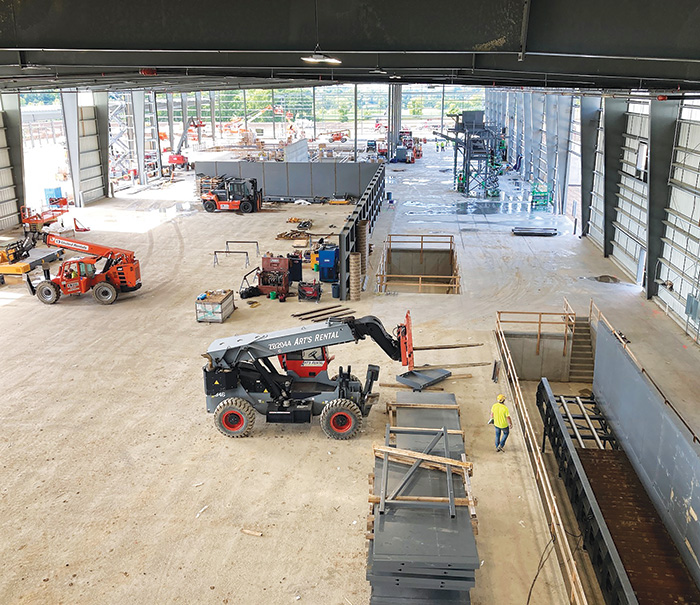
You should focus on many factors for different reasons when selecting the project site. This includes:
• Proximity to your operations to limit drive time and accessibility
• Ideal location that has access to the right roadways and thoroughfares to get your material in and out of the facility effectively
• The site should be properly sized for both facility and project needs by taking account of access roads, stormwater controls, easements, wetlands, or other unusable areas and setbacks
• Choosing a location that has a suitable employment pool nearby
• Access to the right utilities from water to power and everything in between
• Proper zoning to allow this type of use
• The site should be generally flat to allow for, but not limited to, scale placement and access roads, building footprint, user access
• If you are going after any LEED certification, the site selection becomes critical for many more reasons
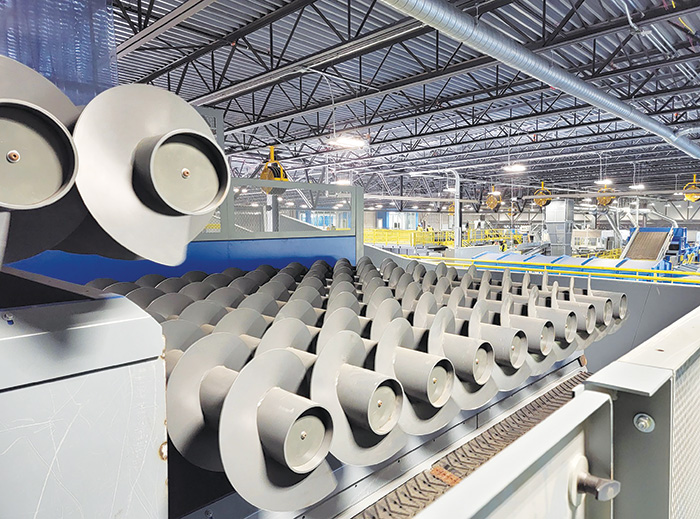
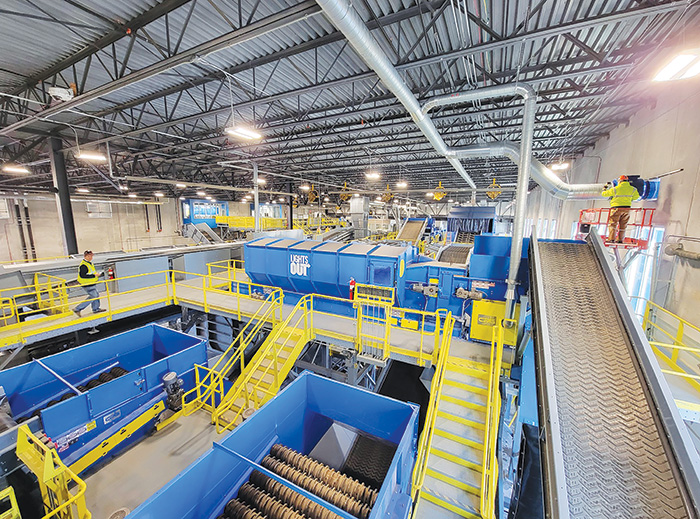
The Building Envelope
Many times, we see owners dictating the MRF building size and then directing the equipment vendors to “fit the system in the building”. Although this is a common approach when retrofitting existing buildings, it can lead to issues down the road. Ideally, you should provide your equipment vendor with a flexible building footprint within a “box” that they can use as a general guideline to efficiently design their system to allow for minimal system turns, excess conveyor belts, vertical layers, and room in and around the equipment for proper maintenance and repairs. At the end of the day, once the facility is turned over, you want to make sure that your operations team can easily reach all the right areas of the equipment to safely conduct their regular maintenance, replacements, repairs, and clean-up duties. This is most easily accomplished if the equipment supplier is allowed input when designing the system.
The need for flexibility when approaching the building envelope comes into play when considering access points around the equipment for forklifts and other machinery and for walkways for employees, visitors, and other guests to access areas of the system. Flexibility also comes into play when it comes to column layout. If the equipment suppliers are told where the columns are, then it limits their layouts. They need the ability to move those around as well.
Long Leadtime Items
In the current construction market, there are several items, such as electrical gear and air-handling units, that can have extended leadtimes up to over a year, so planning ahead is important for any critical path items. While MRFs require a substantial timeline to build (around 12 months or more), it is still important that the long lead items are identified around the 30 to 50 percent design timeframe so they can be procured and delivered to the project site on time or early to avoid significant schedule delays. This process also comes into play while considering certain permits and utilities required for the project.
There are many long lead items that your team needs to stay ahead of early in the design phase to keep the project on track. This is a good reason to have the construction team engaged early so they can help identify the long lead items and actively work to get them ordered.
Experienced AEC Team
Owners often hire Architecture, Engineering, and Construction (AEC) teams that are perfectly capable of building, but may lack solid waste experience. If the firms do not have experience working with equipment vendors and MRF operators, they more than likely do not know what questions need to be asked and addressed along the way. These facilities are not just big, metal buildings that can simply be placed on a site. This is a complex operation with complex equipment that is meant to function at a high level for the next 20 years. Common mistakes that we see are:
• Improper foundation design
• Improper concrete slab design for tipping floors
• Foundations installed for equipment
• Pits not properly designed
• Power drop in wrong locations
• Insufficient access around the equipment for maintenance or future upgrades
• Poor coordination between the fire sprinkler system and the equipment
• Incorrect or poorly located access points
• Inability to modify or expand the building for future needs without significant rework
There are several firms in the U.S. that have decades of experience designing, constructing, or design/building MRFs. Do yourself a favor and work with them. It may appear that they will cost more upfront, but they will save you time and money during construction, all while making your facility more operational and cost efficient—enhancing durability of your MRF for many years to come.
Part 2: Designing MRF Equipment and System Processing
These systems are meant to provide communities and MRF owners with years or decades of service. When designing a new MRF, there are several considerations to make early in the process. Everything from traffic flow and employee safety must be a point of focus from day one.
One of the most impactful decisions to make during design is choosing an experienced equipment vendor that has expansive hands-on experience within the industry, catering specifically to operators of sorting systems who will help guide you through the entire process. MRF systems are complex and expensive investments which is why choosing the right partner matters. The following are important factors to consider during this planning phase.
Big Picture Project Objectives
When you are considering a new MRF, you must first have a solid understanding of what your project objectives are. A lot of detail comes into play with this. There are several questions that are helpful for MRF vendors to know when you first engage with them:
• What space will be dedicated to the MRF?
• What is the material characterization?
• What commodities will be recovered?
• What is the annual tonnage to be processed and within what operating days/hours?
• What is the system budget?
• Where is the material coming from and how long are material contracts?
• Are there foreseen changes in tonnage or material to be processed?
• Is it more important to my project to save on CapEx or OpEx?
Flow Optimization
Once the questions above are addressed, an experienced MRF vendor will work on a material flow diagram. This schematic is done early to give a road map of the facility layout. With the material characterization, a mass balance will be created to identify any system bottle necks to ensure equipment is operating at efficient tonnages. Geographical factors can play a big role in flow optimization, as many regions are subject to severe weather changes throughout the year. Some regions must also account for material changes if they are a destination or a college city for example. These considerations must be accounted for early in the design process to ensure the system is optimized throughout the year.
The main responsibility of the MRF vendor is to have a streamlined process with efficient conveyance of material, which can be impacted by the building space and traffic flow. The schematic material flow diagram is modeled with 3D engineering software to assist system placements within the structure. This model will also be used early to consider system placements in coordination with tip floor, bale storage, employee lounge, bathrooms, viewing platforms, operating rooms, air compressor area, ingress and egress, residue and glass load out, direct bale feed, and all other necessities. This can be accomplished with the MRF vendor working closely with the building contractor with excellent communication across all coordination channels.
Access
Being able to oversee all sorters on the same platform from the operating room is ideal for safety. It is fitting to have your sorters enter and exit the sorting platforms at the safest location, closest to the employee breakrooms and in one location. Maintenance access must also be a point of focus at the beginning of project planning. A specialized piece of equipment, such as a lift or crane, may be needed to maintain and change parts for certain equipment. With this, there must be access from the floor and around the equipment, including any pits, to perform proper upkeep and maintenance. An experienced MRF vendor will provide a maintenance matrix that thoroughly outlines access to all equipment and the tasks that should be performed daily, weekly, monthly, and annually to keep the systems operational and safe.
Future Planning
Proper planning and the creation of system modes will allow flexibility for future material changes or needs. For example, there could be a residential mode and a commercial mode that can run on the same system. By using reversing conveyors and recipes, the same system can be used for different applications. If there are plans to add more tonnage in the future, it is important to think ahead and leave space for an additional line or equipment.
It is best practice to plan upwards of five years on material changes to account for flexibility and space. When possible, it is ideal to oversize equipment like screens, balers, eddy current separators, and optical sorters so these machines do not become your future bottleneck. Upsizing air compressors is also a wise investment to consider as automated machines like optical sorters, that rely on air, are being incorporated into systems as personnel becomes harder to find.
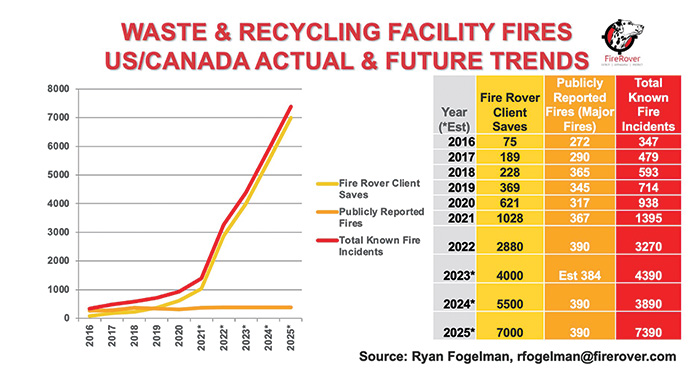
CapEx Versus Opex
Pay now or pay later? Many times, a system with higher CapEx will have more automation, therefore, fewer manual sorters, higher recovery, and purity of commodities with less OpEx. A system with lower CapEx will require more manual sorters and likely will not produce as good of results as automated MRFs and will have higher OpEx. An important factor to consider is the decline in the availability of manual sorters, overhead and retention costs. Because of this, automation is becoming more and more popular.
Part 3: Fire Prevention and Early Detection
The waste and recycling industry has been dealing with traditional fire hazards since the beginning of time. Then came the lithium-ion battery threat that revealed itself in 2018 in the form of increased fire incidents across the globe. The industry reacted with a three-pronged approach of operational best practices, consumer education, and innovative technologies.
Even with this focus, it is clear from the past three years of reported fires that we are still in the heart of an epidemic causing havoc in our critically important waste and recycling infrastructure. From an expert perspective, we have made it through the most challenging part, which was getting our arms around the initial and continued scope of the problem. This problem is not going away. In fact, the number of lithium-ion batteries forecasted to enter the waste and recycling streams is only growing along with hotter and dryer environments, which leads to a breeding ground for increased fire incidents.
The fact is having fires is okay if you can quickly catch and safely suppress them before they become a major incident. Several industries have inherent fire risks in their operations. These industries typically have some sort of protection that makes this risk manageable. Following is the recommended approach when lowering your operations’ risk profile.
Prevention
The most important part of fire prevention is to develop a plan of action. Prevention is the basic blocking and tackling and should include all components of minimizing the potential number of events that can occur at your facility.
Internal Response
Early detection is the key to catching and mitigating a fire early. The goal is not just to catch a fire when there are flames, but also to understand that there are situations where hot spots can be cooled before they flame. The goal is to set the tripwire as early in the process as possible. This can be done through top-grade thermal detection in combination with smoke, optical flame detection, and advanced data analytics—all coupled with a highly trained agent who is able to weed through false positives to fight only the incidents that need fighting.
The most concerning fact to me is that as of today’s article, the Fire Rover early detection and fire elimination solution is actively installed in approximately 500 MRFs, transfer stations, scrap metal yards, electronic waste sites, construction and demolition facilities and hazardous materials sites across the globe. Additionally, the fact that 2022 was (and 2023 is forecasted to be) the worst year for reported fire incidents since I began reporting them in 2016, proves we are not out of the woods yet (see Figure 1). On the contrary, we are heading down a path where investments in solutions like the Fire Rover are considered ‘critical’ to successfully responding to the fire hazards that continue to hit our waste and recycling streams. We need a funding mechanism like the government or the battery manufacturers to help pay for the costs they have created.
Professional Response
Another essential part of the internal response is to prepare the professional response. Investing in proper equipment for the fire department to use onsite can be a huge timesaver and lifesaver. Even going as far as having attached and rollout hoses so the firefighters can immediately start applying suppressant to the affected area can make a huge difference. Most importantly, having an active relationship with your local fire department is imperative.
Elevate the Final Product
When building a MRF, the goal is to end up with a facility that operates efficiently, requires minimal repairs and downtime, and flexibility to accommodate future equipment upgrades and modifications. Actively seeking out and incorporating practices from experts who focus on design, building, and managing MRFs will elevate the final product of your new, successful facility. | WA
Ashley Davis, MBA, is the Director of Sales and Marketing for CP Group. She is third generation of the family-owned company. She manages the sales and marketing teams and oversees all sales and brand objectives. Her focus is on sales layout developments and delivering high quality customer experience through all brand touchpoints. She can be reached at www.linkedin.com/in/ashleydavispawlak/. For more information, visit www.cpgrp.com
This article originally appeared in the August, 2023 issue of WasteAdvantage