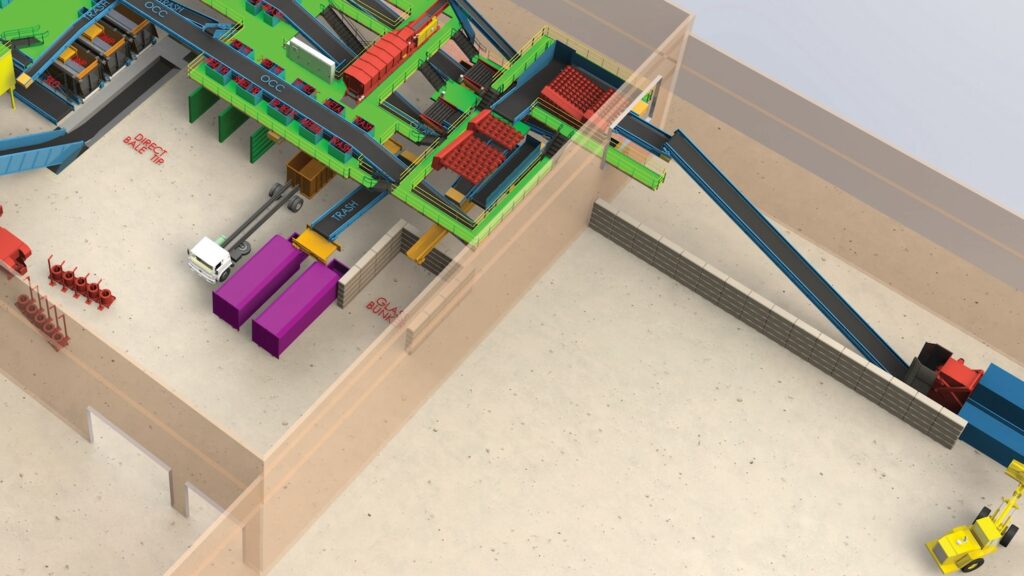
The modern MRF has no presort, a reduced headcount, high-volume screening and automated sorting of commodities; Reduced OpEx with increased recovery and purity.
Building a modern MRF involves embracing innovative design principles, leveraging advanced equipment, and fostering effective stakeholder communication. CP Group’s trusted expertise in creating successful MRFs has revolutionized recycling operations, reducing operational costs, improved recovery rates, and enhanced sustainability. As the recycling industry continues to evolve, CP Group remains at the forefront, driving innovation and making significant contributions to the future of recycling.
Successful MRF Design
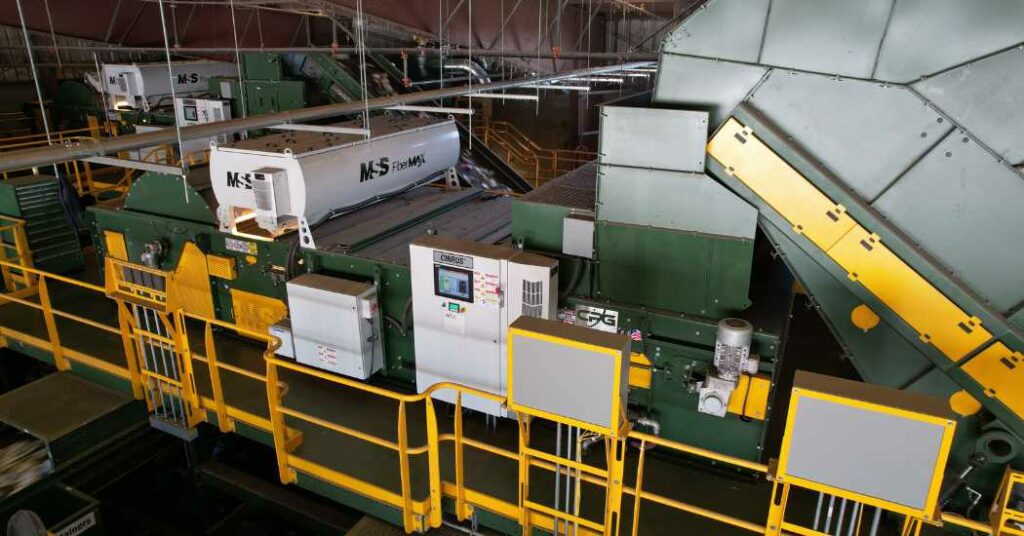
Building a successful MRF entails working closely with an experienced MRF designer/manufacturer. Success lies in part with supplying accurate material characterizations, defined recovery goals and communication.
Modern MRF Design Principles
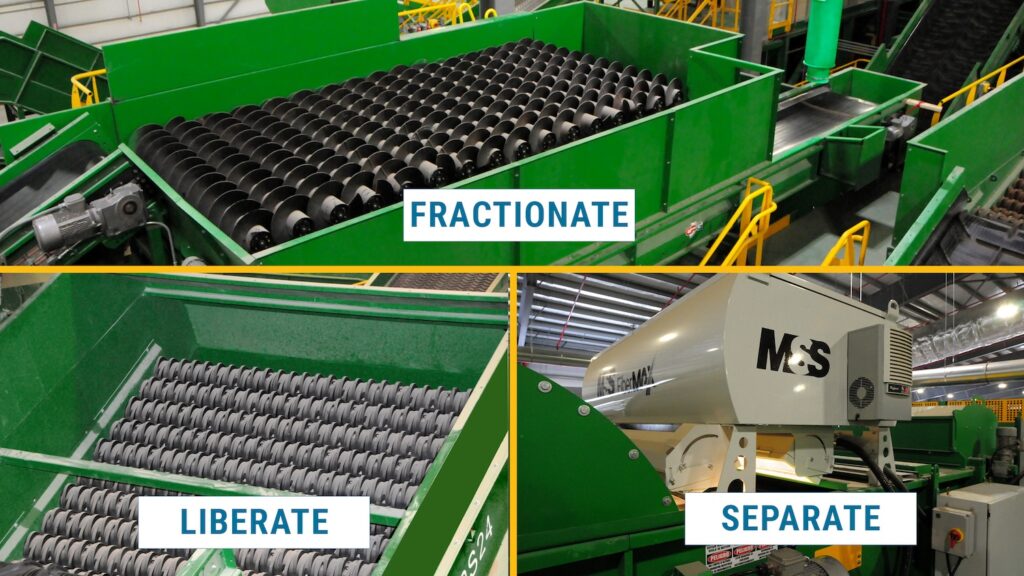
Fractionate, liberate and separate are the design principles coined by CP Group that shape the modern MRF design.
What Equipment Is In A Modern MRF?
Low headcount and maintenance, high recovery and purity and system data intelligence are achievable with modern MRF equipment, outlined below.
Proper System Feeding
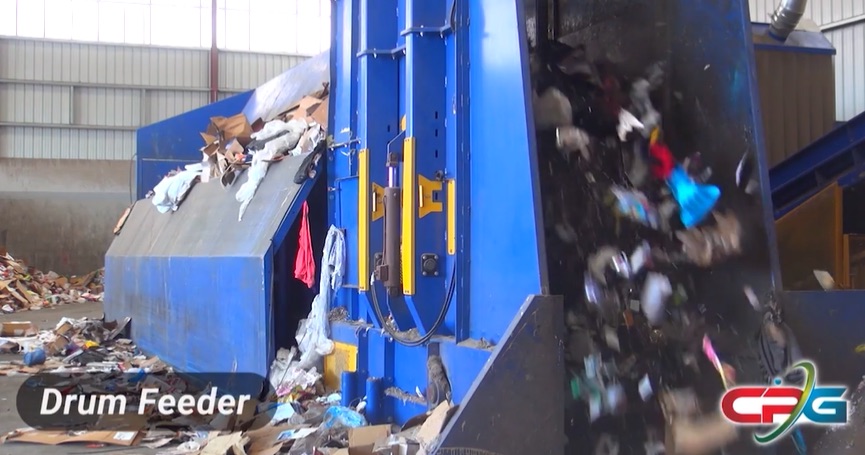
Although not a new concept, proper system feeding is imperative. The Drum Feeder fractionates and liberates material to feed the system consistently and enables downstream efficiency.
Eliminate The Presort
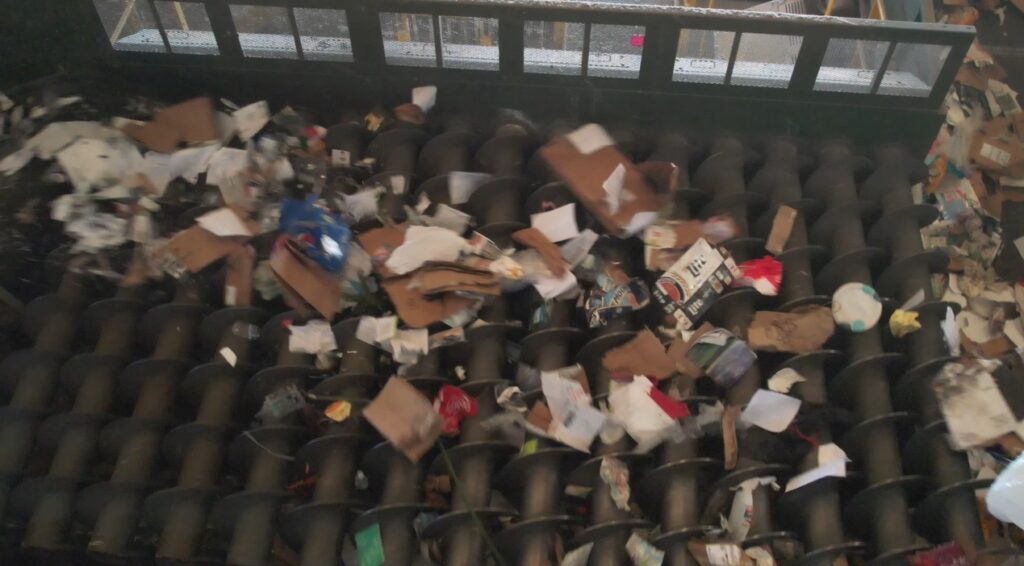
CP pioneered eliminating the presort with the CP Auger Screen, a new nonwrapping, high-volume screen which needs no presorting.
Primary Auger Screen
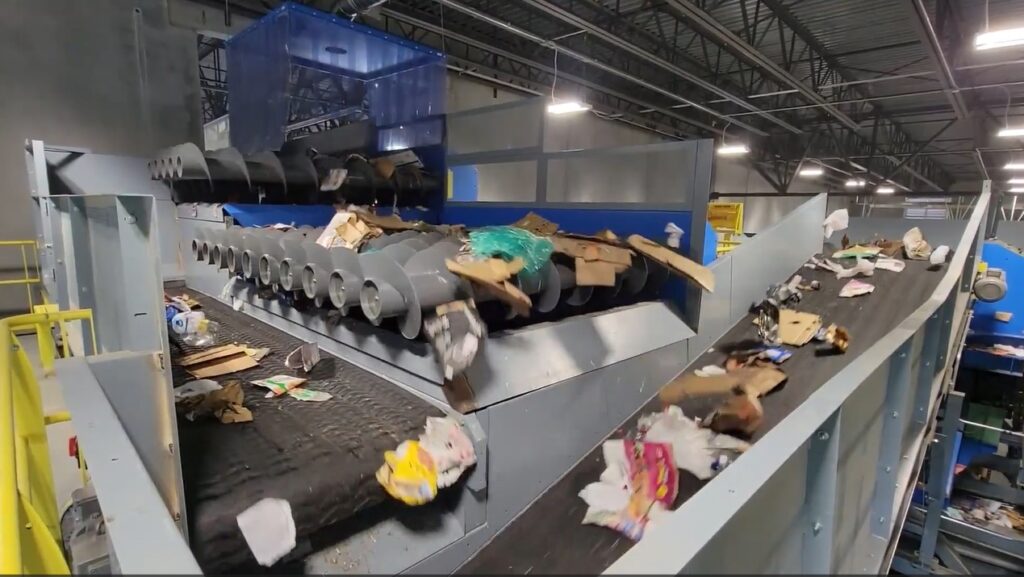
This nonwrapping machine fractionates material with cantilevered augers. Before any sorters, this machine removes the small fraction, including needles and sharps, to improve safety.
Patented OCC Auger Screen
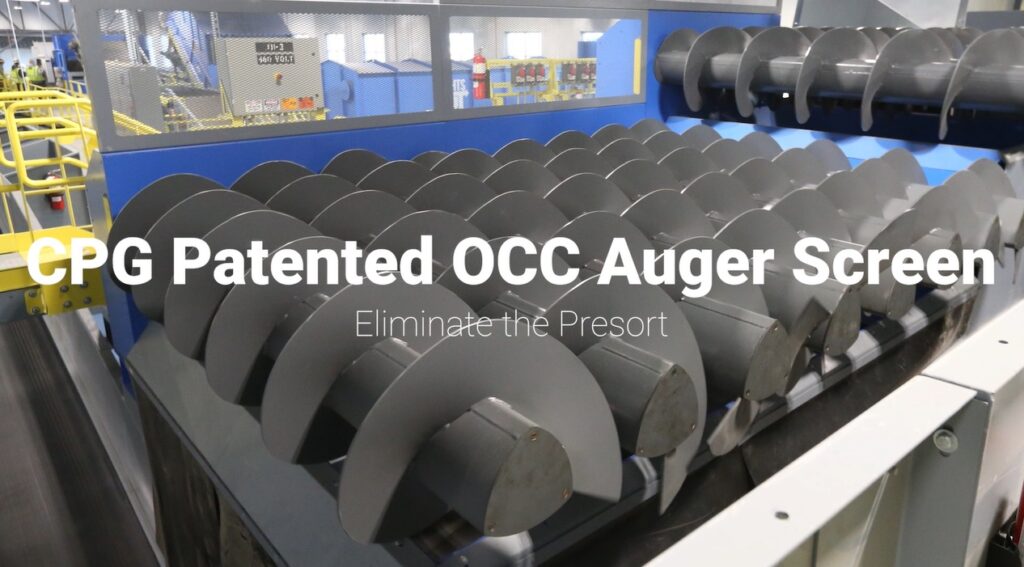
Patented nonround augers fractionate and agitate material to create a clean OCC product, omitting the need for an OCC Screen. No presort, nonwrapping and low-maintenance.
NWRA 2022 Innovator Of The Year Award
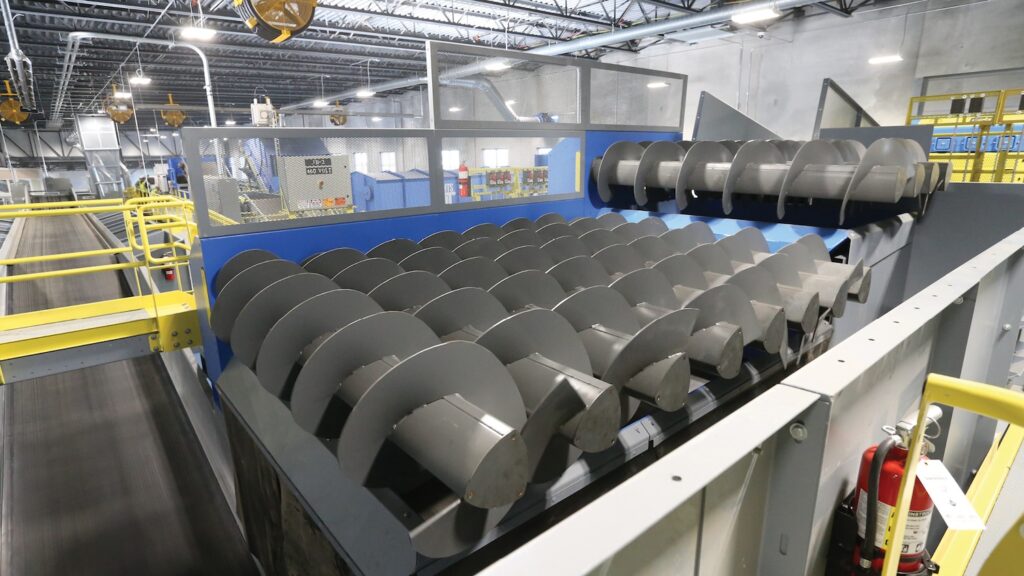
Award recognizes recycling equipment designers that challenge and advance recycling operations. It celebrates innovation in design and manufacturing that increases the effectiveness/efficiency of recycling operations.
Glass Breaker Screen
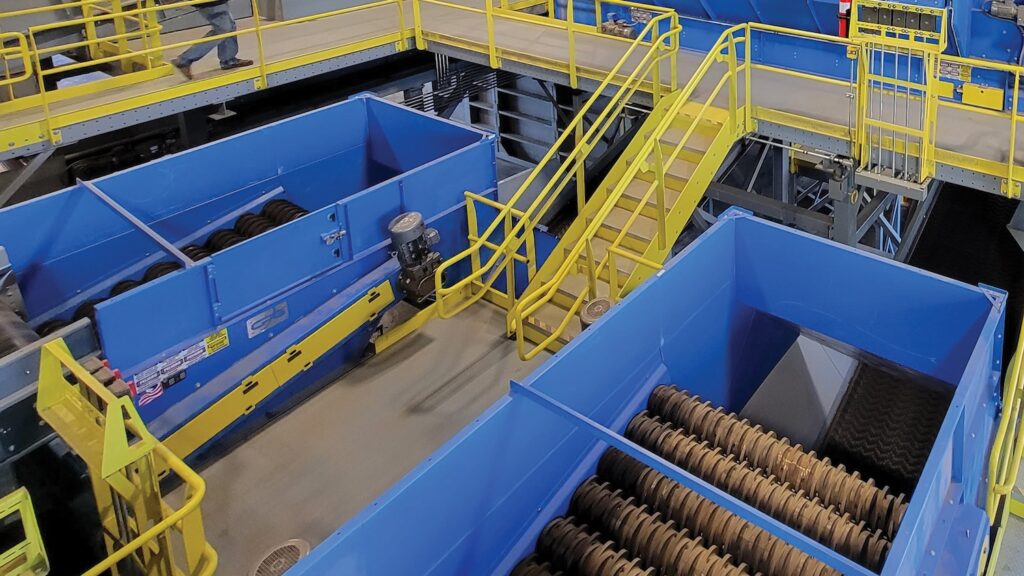
The trusted CP Glass Breaker discs are specialized, long-lasting cast-chromium steel discs which fractionate and remove fines and glass from the stream early in the process.
AW Screen (Anti-Wrap Screen)
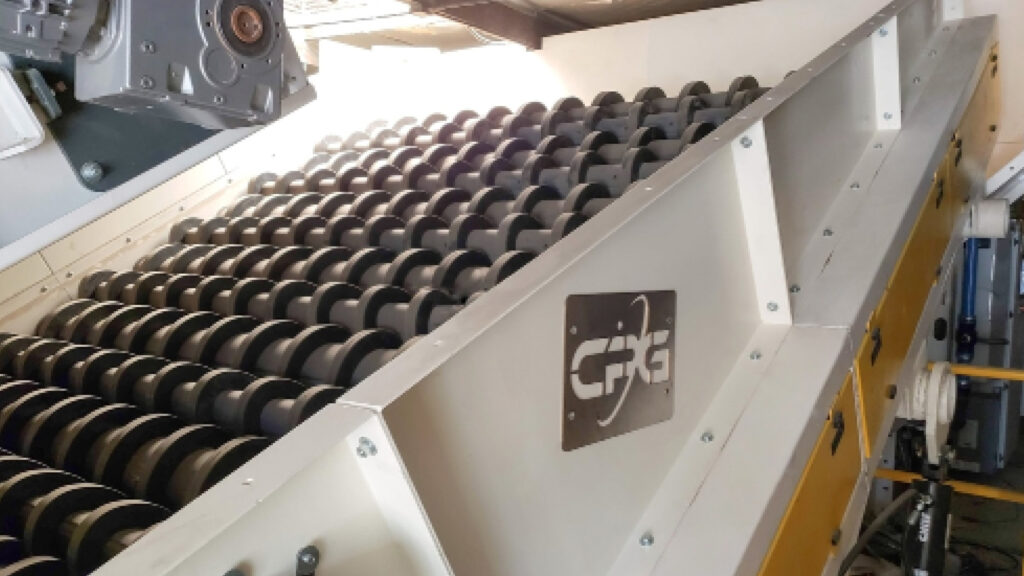
Modernized large paper 2D/3D screen mitigates wrapping with large circumference shafts and smaller openings. Liberates 2D from 3D material at high volumes.
CP Screen Liberates 2D from 3D
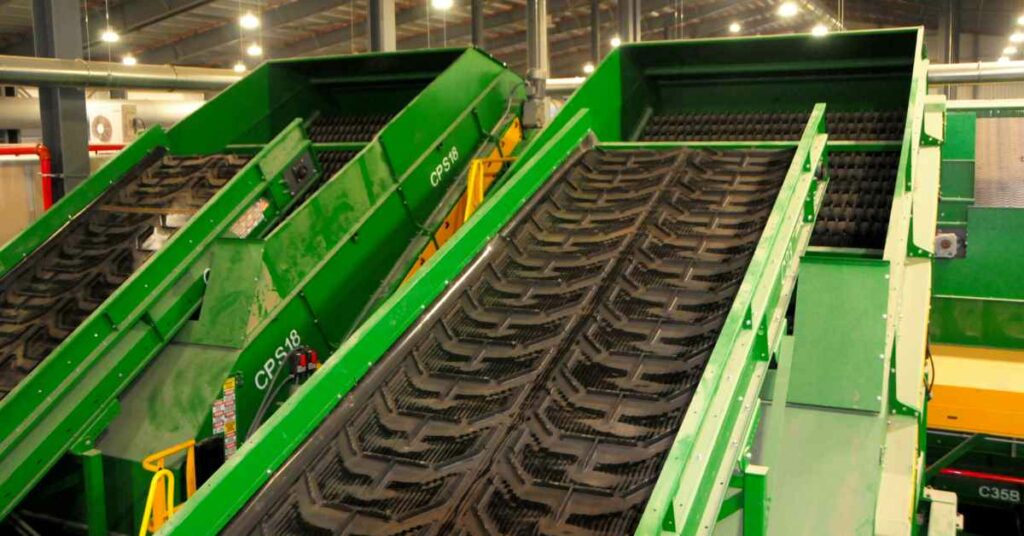
By agitating materials with high amplitude disc screens, glass/dirt/fines are liberated from the 2D/3D commodities and captured by the third cut. Separates small fiber from containers.
Sorting Success
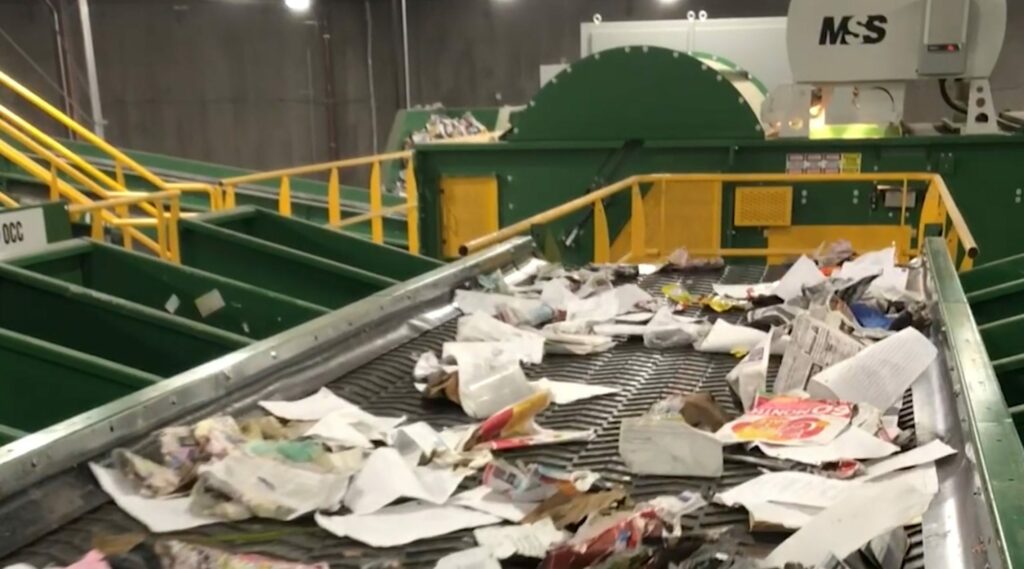
Success lies in pairing the right sensor technologies with the right extraction method. NIR, color, metal and vision sensors can pair with air or mechanical extraction.
MSS CIRRUS FiberMax™
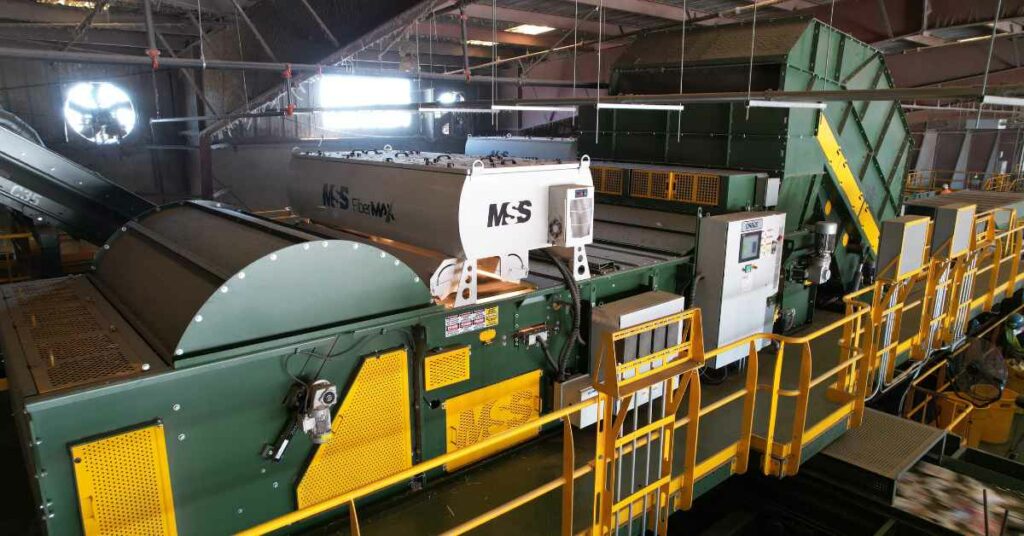
These high-volume NIR fiber optical sorters have belt speeds processing at 1,000 feet per minute with the capability of 1,000-plus picks per minute—the fastest in the industry.
MSS CIRRUS PlasticMax™
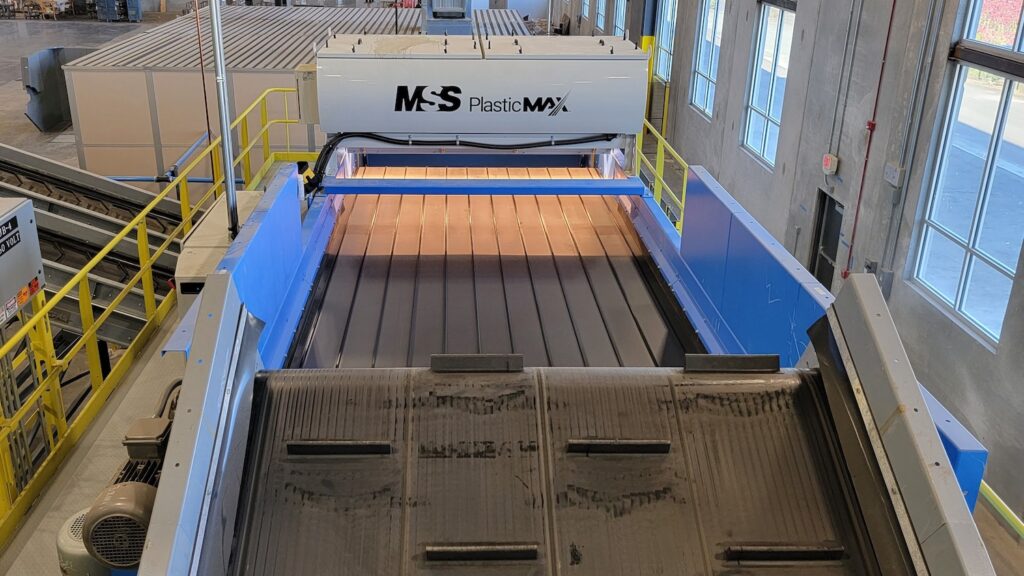
Optical sorting separates and recovers PET, HDPE and mixed plastics. Combines high-resolution NIR and color spectrometry with metal detection.
MSS Vivid AI – Automated QC
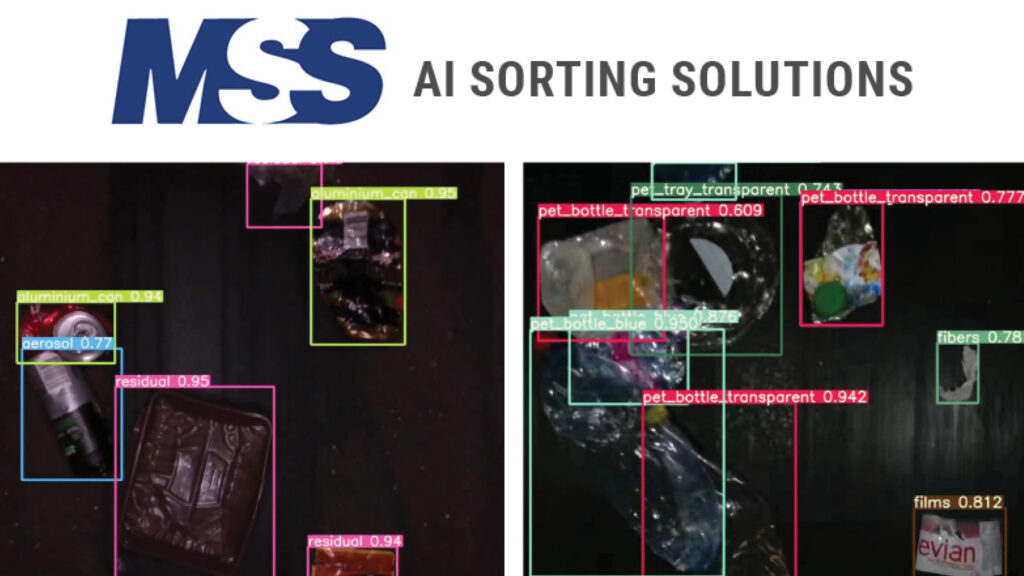
Announced this May, Vivid AI combines Recycleye AI and MSS system capabilities to see and sort more material classifications not previously possible.
MSS Vivid Air
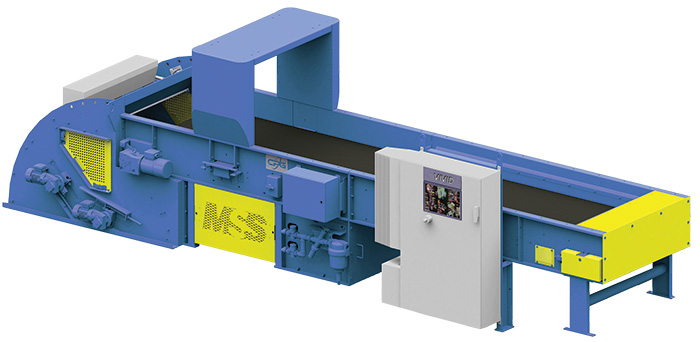
Combines the powerful Recycleye AI vision with the field-proven MSS air ejection system to sort material at the highest volumes without restrictions on picks per minute.
MSS Vivid Bot
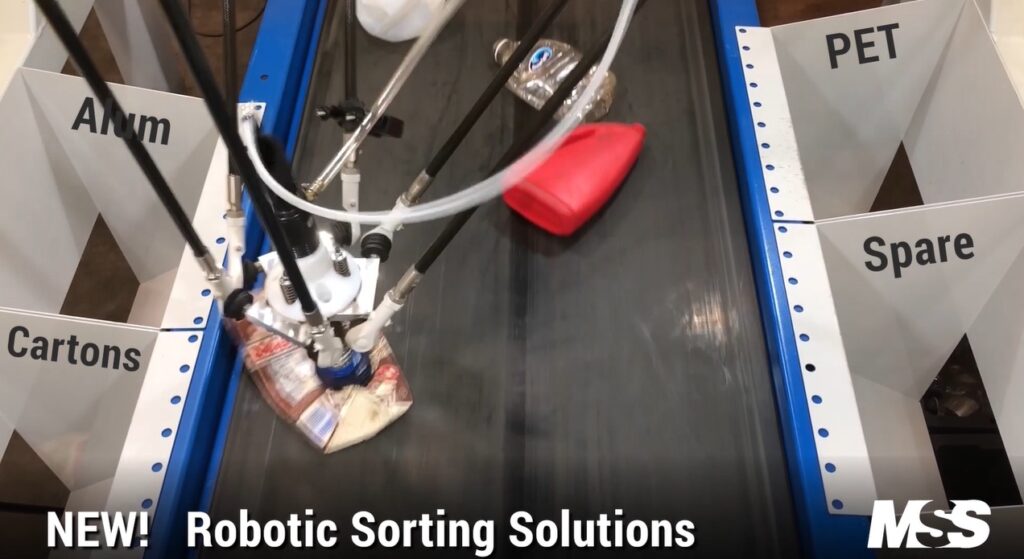
Robotic extraction solution for tight retrofits and multiple separate sort categories sorting applications.
MSS Vivid Vision
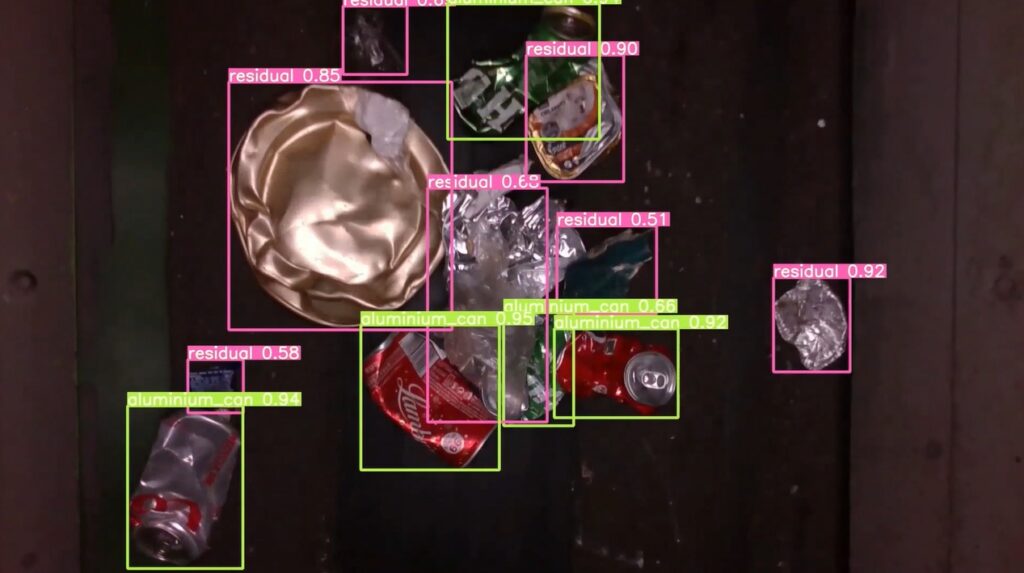
Take full advantage of the AI’s powerful statistics and data monitoring tools.
Low Maintenance, High Performance
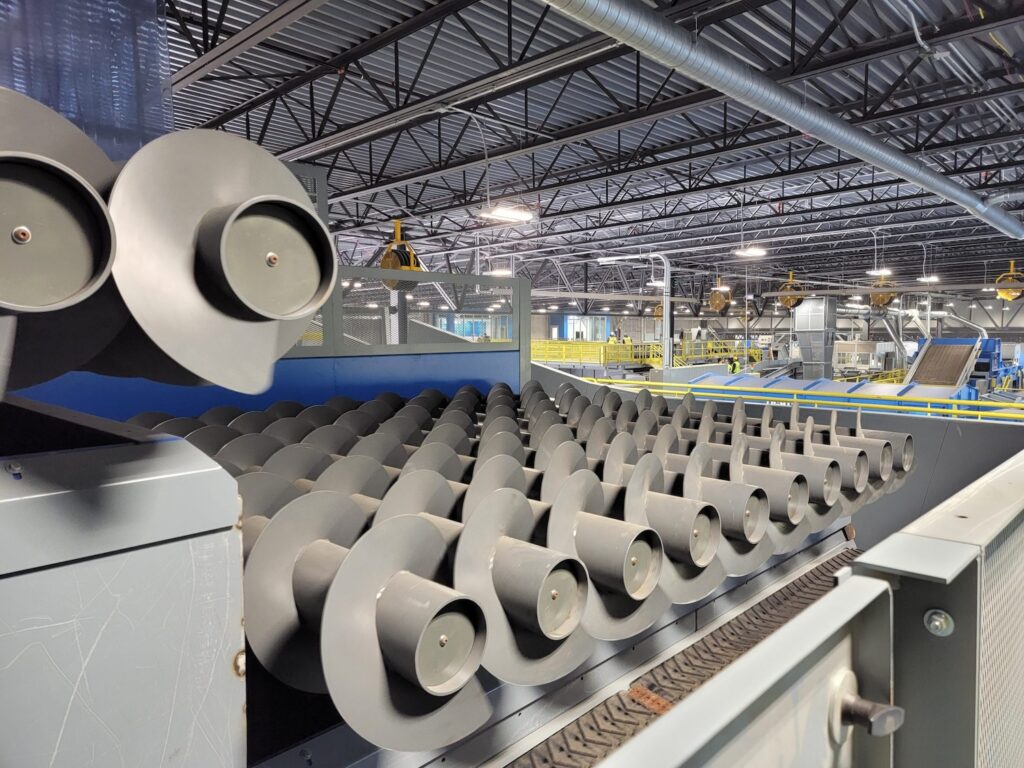
Modern MRFs utilize nonwrapping cantilevered auger screens and anti-wrapping disc screens to fractionate/liberate material and high-capacity optics and AI to make sorting decisions (low headcount).
Building a modern MRF involves embracing innovative design principles, leveraging advanced equipment, and fostering effective stakeholder communication. CP Group’s trusted expertise in creating successful MRFs has revolutionized recycling operations, reducing operational costs, improved recovery rates, and enhanced sustainability. As the recycling industry continues to evolve, CP Group remains at the forefront, driving innovation and making significant contributions to the future of recycling.
This article originally appeared in the issue of Recycling Today